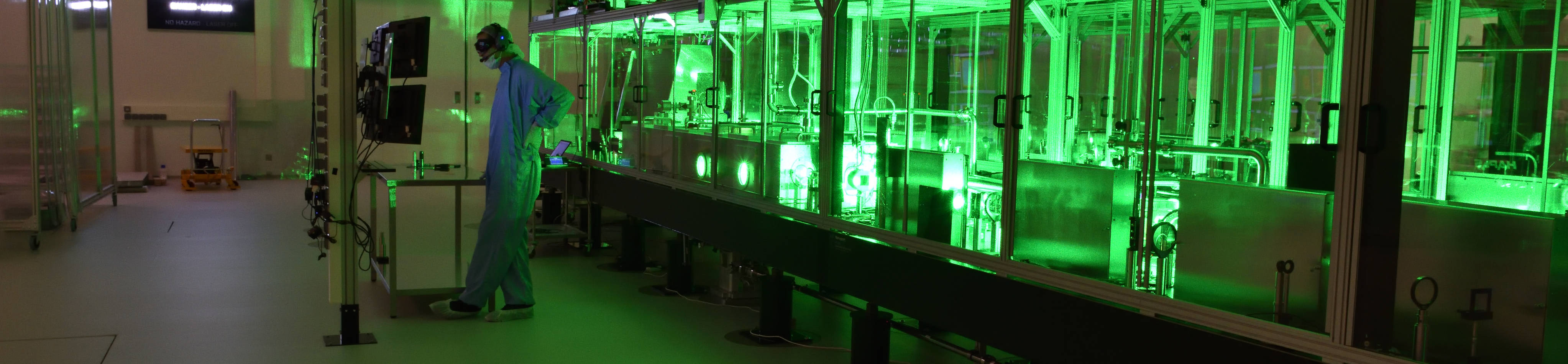
New manufacturing approach for grating targets results in enhanced laser absorption
The article “Fabrication of micrometre-sized periodic gratings in free-standing metallic foils for laser–plasma experiments” recently published in High Power Laser Science and Engineering of the Cambridge University Press describes a novel manufacturing approach, specifically developed in order to allow multi-step patterning process of thin self-supported metallic foils (of 3 μm and 10 μm), and testing of the resulted structures. The result is an enhanced laser absorption on this type of solid targets. The group working in the ELI-NP Target Laboratory, one of the contributing groups to this article, is involved in IMPULSE Work Package 4 (key technologies & enhanced experiments).
To improve the efficiency of high-power laser interaction with matter, the experiment focused on changing the characteristics of the “targets”, the generic name of the materials used in such interactions. This is achieved by changing the surface characteristics of thin metallic foils, specifically by creating rectangular or sinusoidal micrometre-sized periodic gratings (see Figure 1), enabling an enhanced laser energy absorption and higher efficiency in accelerating charge particle beams compared with planar thin foils of similar thickness.
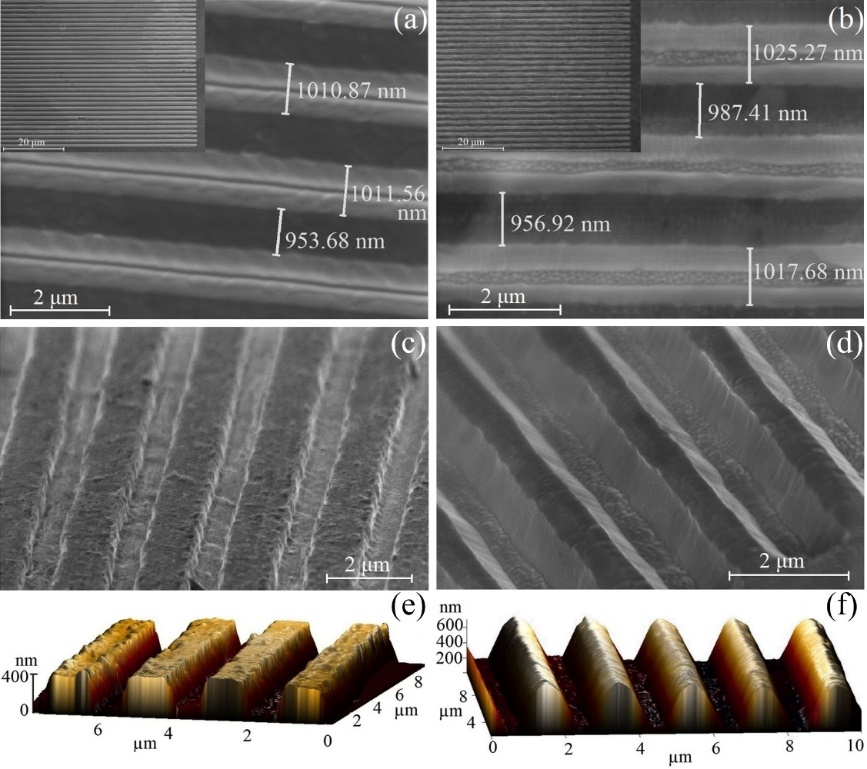
Figure 1. SEM images of grating patterns in Cu (a) and Au foils (b) obtained after complete optimized fabrication process; darker parts correspond to non-etched areas, brighter parts to etched areas, respectively. Insets show an overview of the gratings. SEM (c,d) and AFM (e,f) images with Cu rectangle (c,e) and Au sinusoidal (trapezoidal) (d,f) shape gratings.
The novelty of this research is in the manufacturing approach: the method is based on several patterning techniques that can be found in most material science laboratories, i.e., electron-beam lithography and Ar-ion milling, given the freedom of fabricating periodic gratings in a wide range of dimensions, nanometre or micrometre scale. The methodology used in the manufacturing process, described in the article, can be further applied to thinner free-standing foils.
“The paper is the result of a fruitful collaboration between two groups, the ELI-NP Target Laboratory, Magurele, Romania, for the fabrication of the gratings, and the Institute of Laser and Plasma Physics, in Düsseldorf, Germany, for their testing,” says primary author Cristina Gheorghiu, Junior Researcher of ELI-NP Target Laboratory. “This partnership is the result of a joint effort with each team contributing with their expertise, resulting in a successful experiment.”
Future research includes additional experimental tests at the Arcturus laser system in Düsseldorf, to complete the information obtained with the preliminary analysis. Moreover, keeping in mind that these processing methods, described in the paper, can be used for yielding micro- or nano-sized gratings with dimensions limited only by the employed lithographic method, other types of structures can be envisaged and expanded for further similar experiments, while the methodology of targets with periodically modulated surface can be tuned for structures with smaller lateral dimensions, height and thinner overall thickness of the substrate.
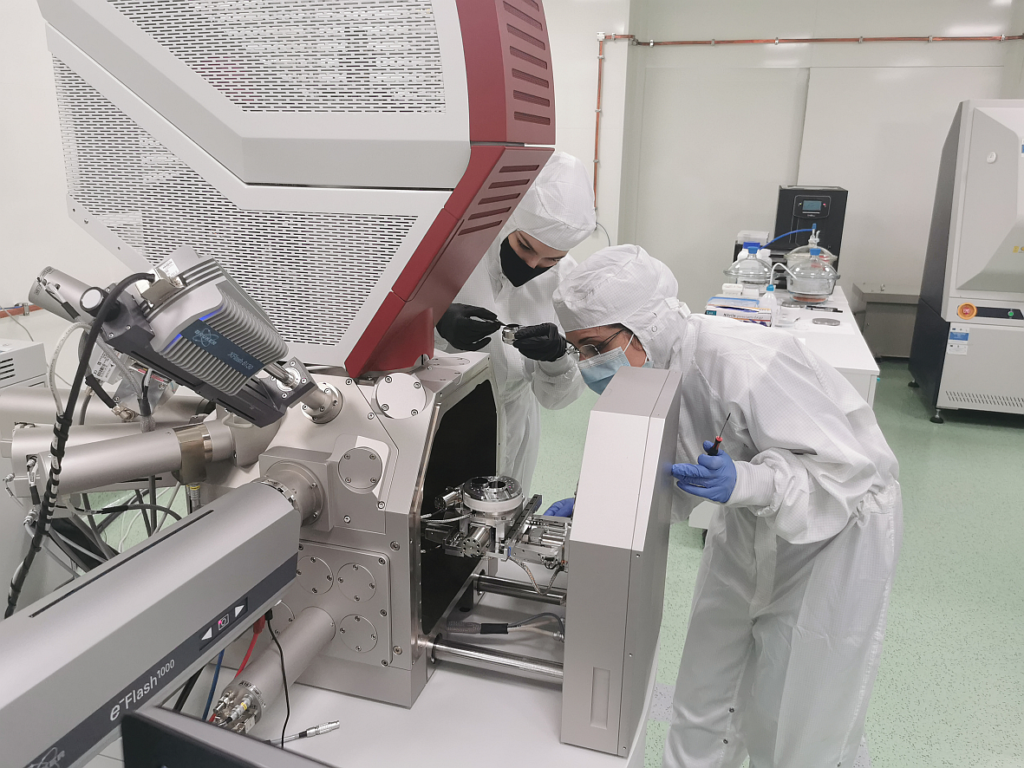
The group working in the ELI-NP Target Laboratory contributes to IMPULSE Work Package 4 which addresses and supports the development of key technologies and enhanced experiments at the ELI Facilities. Task 4.2 specifically encompasses the laboratory side and from the experimental part, such as analysis and definition of the target needs of ELI’s users, the definition of the appropriate supply strategies, and the evaluation of the present manufacturing capabilities.
Moreover, given the scope and strategy for IMPULSE as a joint project, it allows the possibility to perform specialised training activities in-house and at partner organisations, to build good practices for target fabrication, and assembly techniques. This is a crucial aspect for all project partners, as it increases the synergies between target fabrication laboratories with the development of state-of-the-art manufacturing and characterisation protocols.
The article was published in the High Power Laser Science and Engineering (2022) 10, E3. doi:10.1017/hpl.2021.57